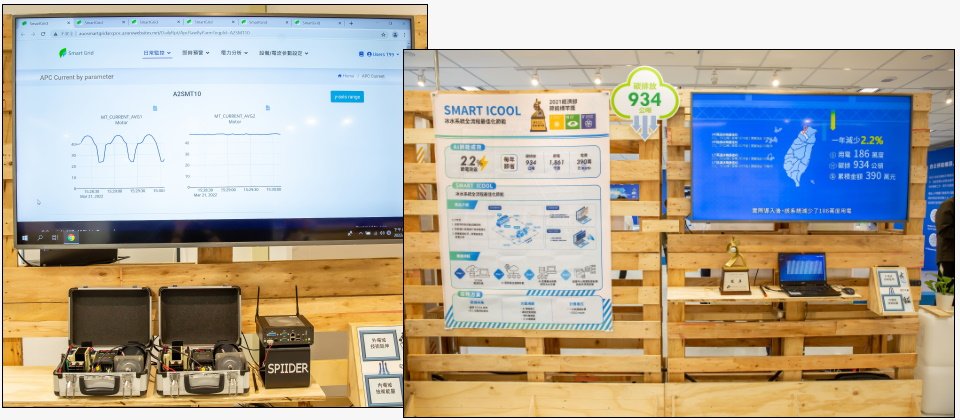
友達內部打造一套Smart Grid智慧電網系統,能夠分析IoT機上盒從機臺設備蒐集的電流等資訊,來做到節源的調控。
工廠智慧化成果 1 老舊機臺自動上傳IoT數據監測異常
3千臺舊型PLC機臺無痛升級IoT
面板廠一臺PLC機臺動輒上億元,改機成本相當昂貴,將20年老舊機臺升級IoT,這是老舊工廠智慧化的第一步。所以友達內部開發IoT機上盒裝置,讓老舊機臺數據蒐集更容易,不只免停機就能安裝,甚至可以做到隨插即用。友達一共部署超過3千多套這樣的裝置到19個fab廠中,共蒐集機臺22萬筆PLC參數,用來監控設備健康狀態,也因此讓停機降低30%,維護成本降低20%,品質良率提升5%,也省下百萬美元的改機費用。
用軟體工具分析IoT數據也加以視覺化
機臺PLC數據擷取出來後,就能透過WiFi回傳到友達自行開發的精準保修平臺進行設備故障分析,並將分析結果以視覺化呈現,另外也會透過MQTT協定將這些數據儲存到雲端資料庫,作為後續大數據分析使用。還搭配友達PHM設備健康管理平臺一起使用,平臺上提供了許多預警功能可以選用,包括有AI異常檢測、健康評估、異常診斷、壽命預估等預警功能。
內建AIoT透過邊緣運算即時回報異常
針對不同製程機臺,友達內部也有提供不同類型IoT機上盒,除了可以蒐集PLC數據,也能回傳各種IoT感測器數據,如電流、震動等,而且不只固定在機臺上,還有移動式版本,維修工程師帶在身上,就能進行設備維護和異常診斷。這臺移動式機上盒更內建AIoT功能,能更即時回報異常,也提供GUI介面,方便人員查看,因為資料不一定需要上傳,即使沒有網路也不怕。
工廠智慧化成果 2 工廠靠機器視覺提升人員、環境安全
用AI視覺偵測加強人員SOP落實
生產中的常見問題是,產線作業員沒有完全按照SOP作業,因為過程中某些操作或動作未依規定完成,就容易產生品質風險,友達內部作法是直接把整套產線作業流程,變成可以用系統方式來監控,將攝影機拍到的畫面傳到附近的邊緣設備上,結合電腦視覺來偵測,例如在切割作業時,從作業員身體肢體動作及姿勢,就能知道這個人有沒有把切割的動作做到位,一旦動作沒有確實完成,系統就會發出警示,要求重做,等動作完成後,才進到下個流程。
廠內環境和作業安全都靠AI加強把關
除了用刷臉管理門禁,友達也把這項識別技術用來提高工廠環境和人員作業安全的監控,還因此打造兩套系統,一套是測距監控系統,一套為穿戴偵測系統,前者可針對維修區域或化學品溢出的區域,使用AI攝影機建立虛擬安全圍籬,並依人員與虛擬圍籬間的距離來管控風險,一旦達警示距離,除了語音提醒還會用Line通知人員到場處理。後者則用在高風險作業環境中,使用機器視覺偵測身體不同部位的穿戴配件,提高人員作業安全,比如身上有無穿戴安全帽、護目鏡、口罩、手套、背心等,並整合到單一個螢幕畫面中,方便管理人員查看。
用影像IoT記錄取代機臺機構巡檢
除了以IoT偵測機臺設備異常之外,友達還採取視覺方式加強機臺內部的機構檢測,在機臺中架設AI攝影機,利用影像來偵測機臺每個重要零組件的健康狀況,也因此,檢修人員不需要每天巡檢和定時拍照,而是改用影像IoT記錄機臺的狀況,以GUI定時拍照取代人員巡檢,因為機構檢查不需關機,也較不容易造成機臺的突發當機 或磨耗影響良率。
工廠智慧化成果 3 從智慧化能源管理邁向淨零碳排
在能源管理上,友達內部打造一套Smart Grid智慧電網系統,能夠分析IoT機上盒從機臺設備蒐集的電流等資訊,來做到節源的調控,透過這樣的方式,每年可以減2~3%的電費。尤其廠務設備用電占全廠用電量60%,其中CDA機組為廠內用電大宗,除了提供數位化報表用電量趨勢分析外,臺中三期廠區還增加能同時監控開機數及各產線CDA用量的功能,一旦產線CDA增量需調度啟動另一主機時,管理者可立即查看與展開相應處置,推估年節電量485萬度。另針對高用電的冰水主機也導入AI技術,透過智慧化管理,來達到最佳化節能的效果。透過這樣的方式,每年可以節省934公噸的碳排放、節電1,861千度,以及省下390萬元的電費。
工廠智慧化成果 4 AOI靠AI影像視覺更能揪出產品瑕疵
用AOI搭配AI視覺提高檢出率且更省人力
過往生產線上採用 AOI(自動光學檢查機)檢測瑕疵品,但AOI設備常受到產品設計不同而影響檢測結果,得再透過人力來進行複判,而人工檢測易受過多變數影響,出錯率高造成更多損失。為了解決這個難題,友達在AOI設備導入AI 技術對瑕疵檢測進行強化,以現有、大量的光學檢測數據訓練AI模型,以AI影像視覺辨識檢測生產線產品,不只複檢人力降低至10分之1,也提升30%分類準確率。友達現場展示了模擬生產線卷對卷AOI機臺的AI瑕疵檢測。
減少AOI瑕疵誤判的關鍵就靠3套系統
一共有3套系統,在友達工廠AOI設備上來使用,線上即時檢測系統、瑕疵管理專家系統,以及智慧分類系統,前兩者都是屬於AOI系統相關,後者則是結合AI視覺瑕疵檢測演算法,友達正是透過這3套系統,幫助工廠來減少生產流程中的產品瑕疵誤判、容忍機差和減少工作量。像是使用者可以透過線上檢測系統,更即時掌握產品的生產狀況,而針對過去瑕疵資訊難以跨製程整合的難題,也能透過瑕疵管理專家系統就能解決,還提供良率預估、自動判斷產品等級等功能。
導入AI智慧分類系統能偵測細微瑕疵
進行瑕疵檢測時,產品會先經過AOI初判後,再透過友達自行開發的一套AI智慧分類系統來進行複判。這套AI分類系統結合多種瑕疵分類演算法,可偵測細微的瑕疵,不論是輕微凹凸型瑕疵、亮態瑕疵或是異物型瑕疵都難不倒它。這套系統不只檢測瑕疵,還提供記錄訓練足跡與建議調參功能,連模型訓練到運行的服務和管理,都能透過它完成。
工廠智慧化成果5 用無人自動搬運車搭配機器手臂自動巡檢
全自動化的設備巡檢作業
不只協助搬運料件,針對工廠設備的巡檢,友達內部也有開發自動巡檢設備,結合AGV無人搬運車與協作機器人,來輔助人員完成一些工廠設備或機臺的巡檢任務。這臺AGV無人車因為使用SLAM技術,可以即時定位與構建地圖,所以現場不用磁帶,也可以達到精準定位。AGV車移動到指定的巡檢位置後,就會啟動車上的機器手臂,手臂上有熱影像鏡頭和OCR鏡頭,可以辨識文字和影像資訊,不像以前都是要靠人員拿紙筆抄表,每天都要記錄這些數值,然後回填到執班記錄表格上,現在透過手臂上搭載OCR影像辨識技術,將要記錄的數值拍照、擷取後自動上傳到後臺系統加以辨識後,就能完成記錄,幾乎全程自動化。
用機器手臂搭配影像辨識取代人工刷洗
在進行TFT面板製程中的乾蝕刻程序時,容易會留有沉積物,過去都是靠人工刷洗去除沉積,不僅花時間,還要額外人力,一年就要花掉數百萬只做這件事,後來友達決定把這個人工清洗作業,改由全自動化機器手臂加上AI視覺取代,不只清洗、洗完後也會拿風槍進行吹乾動作,都靠這隻手臂來完成,再透過影像視覺來檢測,針對不合格的地方,加強清潔作業,確保沒有殘留物。
80um微粒成像靠整合AOI視覺的協作機器人來揪出
光罩製程對面板製程相當重要,只要光罩上殘留一滴點灰塵,就會大大影響曝光,而影響產品良率,但過去為了找出影響不良率的地方,友達費盡心思,因為顆粒度太小,肉眼根本看不見,通常得放大成數千倍之後的80um的微粒成像才能看見。為了解決這個問題,後來友達改以機器手臂搭配AOI顯微鏡,來檢測光罩上的微粒,由AOI鏡頭定位出座標後,再由手臂進行光罩的清潔作業,之後再搭配AOI鏡頭進行複判,確保所有地方都有吹乾淨,透過採用自動化作業,不只每月人力工時減少80小時,光罩搬運多增加300片。
熱門新聞
2024-04-30
2024-05-01
2024-04-29
2024-04-29
2024-04-30
2024-04-30
2024-04-28
2024-04-29