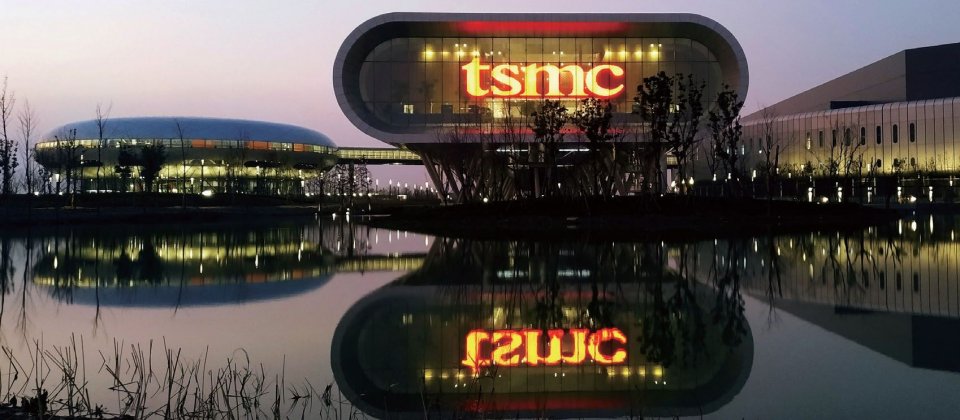
台灣積體電路製造股份有限公司
「台積公司一直用IT重新定義半導體的製造與生產。」台積公司資訊部門一位主管沈文冰的這句話,點出了IT在台積數位轉型大變革中的關鍵地位。在2020年底,台積電有史以來舉辦首次線上IT徵才活動,罕見地揭露了多項推動數位轉型的新戰略和布局。這不是台積電IT第一次大變革,而是30年來的第三度革新。
創造出半導體製造代工服務模式的台積電,非常清楚製造服務業的本質是服務,早在1996年就提出「虛擬晶圓廠」概念,更推動企業組織再造,從生產導向的組織型態,轉變為以服務為本位的服務型組織,要求技術人才要具備行銷技能。
IT,就是讓台積順利將各種製造服務轉為自動化的關鍵。在1996年,台積為了將後勤和財務資訊轉換成管理資訊來輔助決策,展開了資訊系統大升級,當年WWW技術才剛點燃了全球網際網路新浪潮不久,台積就能運用當時的網路技術,推出了全方位訂單管理系統,讓顧客透過電腦網路連線取得訂單和產品生產資訊,這也是半導體代工產業的創舉。1999年更推出供應鏈管理的資訊服務,可以讓客戶透過網路下單、即時查詢晶片生產進度和出貨狀況,早在30年前,台積電就採取了現在網路電商慣用的銷售形式。
由於當時台積早已高度電腦化,許多業務相關軟硬體系統和生產設備,都面臨了2000年年序問題的挑戰,所以,台積電在1997年發起了Y2K專案,提前因應,順利度過Y2K危機。
2000年:智慧製造第一階段,從半自動邁入全自動化
2000年台積晶圓生產製造型態,從過去的半自動,邁入了全自動化時代。
台積電也持續投入電子商務,以成為客戶半導體產品生產的虛擬晶圓廠為目標。不只是可以讓顧客透過網際網路,來進行從晶片設計構思到完成晶片驗證的程序,也推出了TSMC-Online 2.0線上系統,可提供互動式查詢晶圓製造相關資訊,不同客戶角色還可以自訂介面。
台積電在2000年推出了設計服務聯盟(Design Service Alliance)的產業生態系合作模式,將積體電路設計自動化領導廠商、元件資料庫和半導體智財供應商,以及產品設計執行服務業者組成了一個生態系。這種生態系合作模式的作法,台積電後來更用來結合到更多個產業生態系,甚至還擴大套用,連雲端供應商都可以納入半導體產業生態系中。
當時半導體吹起產業解構趨勢,台積看好網際網路技術會推動無阻力事業流程的發展,更加速解構。所以,台積電更在2000年首創eFoundry(後來,台積電用EFOUNDRY來稱呼這個理念所建立的平臺和服務)服務理念,要將更多客戶服務內容,都延伸到網際網路上提供,建立更即時便捷的溝通模式。IT成為台積改造對外服務的關鍵基礎。
這個eFoundry服務(網際專業積體電路製造服務)的基本架構,包括了三大類用途的系統,分別是設計合作、工程合作和後勤合作的系統,整體是以網路為基礎所打造的一套服務系統。例如2002年報就指出,台積電的設計服務,就提供了線上技術資訊查詢服務,客戶能下載台積公司技術文件,來確保製程一致性與包容性。
這個台積電的eFoundry服務,更透過網際網路提供到一天24小時,每周7天的持續服務水準。2011年報指出,設計合作上可以提供每一設計階段準確與最新的設計資訊,工程合作上則可提供客戶晶片良率測試及可靠度相關的工程資訊,而後勤合作可以做到一天提供3次,客戶晶片在工廠封裝測試及運送的多項後勤資訊。
不只用於對外的客戶服務,在台積電發展第一階段智慧製造過程,內部製程和系統也善用IT。台積從2001年初開始建立企業供應鏈管理系統,2002年更有多項改善整體供應鏈效能的跨部門專案,結合IT、資材、財務部門和工廠運作資料,如線上供應(Supply On-line)系統,可整合所有供應商相關資訊給供應商,降低了原料存貨水準。或像是原物料計畫管理系統(Materials Planning Management System, MPMS),來改善生產物料的需求預測,降低缺料的風險。
後續幾年,台積電更持續在運籌管理、生產時程管理、存貨管理、知識管理上善用IT來提高效率。2005年時,物料企畫及庫存管理上持續改善,已經可以透過每周資料更新,有效整合資材與其他相關單位的供需資訊,2007年,繼續精進物料及庫存管理,透過即時資料更新及報表系統,能有效地整合資材及其他相關單位的供需資訊,來提升對物料需求的預測,以利採取快速和正確的因應措施。
為了提供積體電路設計者一套精緻的設計基礎架構,台積電在2008年時,創立了「開放創新平台」(Open Innovation Platform,簡稱OIP),當時納入了電子設計自動化(EDA)流程、通過矽晶片驗證的資料庫和矽智財、模擬及驗證用的設計套件,如製程設計套件(PDK)及技術檔案。雖然,這不是IT主導的研發成果,但是IT協助打造了派送相關資訊到使用者面前的通路,後來在2018年時,台積電更直接改在雲端提供虛擬晶片設計環境,IT的資訊基礎架構能力,更成了建構這個虛擬設計環境服務的關鍵。
2012再次變革,智慧製造邁入第二階段,發展整合平臺和大數據
2012年,台積電的智慧製造邁入了第二階段,進入整合平臺和大數據分析的時期。在工程效能優化上,除了利用先進機臺控制(Advanced Equipment Control)與即時缺陷偵測(Fault Detection)之外,也開始運用大量工程資料探勘(Engineering Big Data Mining)、中央管理製造平臺(Centralized Operation Platforms),來優化機臺、製程和良率。後來,更發展出利用大量工程資料協助決策分析的「智動化」系統(Intelligent Automation System),來維持機臺高效穩定運轉。另外,在2014年報中透露,台積電也開始導入智慧化行動裝置,由IT開發內部用的行動App。
2016年:智慧製造第三階段,引進各種新科技,更要靠AI全面數位轉型
台積電早在2011年就開始嘗試將AI技術導入晶圓製造,研發智慧化生產流程,2015年報更揭露了機器學習優化工程效能的成果。從2016年開始,台積電全力擁抱各種數位新科技,不只是智慧製造,更決定要用機器學習和AI推動全面數位轉型。
台積電的下一代智慧工廠,就導入了行動應用、MR、IoT、大數據和AI技術。IT軟體開發策略也採取Mobile-First和Cloud-First,靠雲端科技作了很多創新。
台積電這幾年陸續提出「精準製造」、「精簡製造」,2015年報提出了「精實與智慧生產」,後來在2016年報則提出了「敏捷與智慧生產」的理念。這些發展背後都大量運用了IT和 AI。
幾年從大數據到AI技術的投入後,台積電2015年報揭露,已經整合了先進資料分析、智慧診斷、自我反應引擎和生產知識等技術,工廠的生產模式,也從「自動化」進一步發展為「智能化」模式,例如發展出了在製品與生產線管理系統,能夠精準控制在製品水位,還配備了彈性化的需求/產能模型系統。在一些成熟工廠中,更利用IoT和智慧化行動裝置,來改善資料收集、良率追蹤、物料傳送和流程的效率。
隨著先進製程發展上,線寬持續微小化和縮短,台積電面臨了更嚴格製程管制的挑戰,台積在製程管制和分析系統上整合了多種智慧功能,例如開發出了精準即時缺陷偵測分類系統、先進智慧機臺控制和先進智慧製程控制,可以即時監控,來準確調整製程條件。另外,也開發出精準機臺腔體匹配(Precision Equipment Matching)和良率採礦分析(Yield Mining)來降低製程變異和潛在的良率損失。為了找出影響產品品質好壞的關鍵,更打造了一個大數據、AI和ML的架構。除了AI技術研發,台積也開始培訓自己的機器學習人才,舉辦全公司性的訓練課程,2017年時開始規畫要在內部培訓300位ML專家。
到了2018年報透露,台積內部AI應用更廣泛了,包括了排程與派工、人員生產力、機臺生產力、製程與機臺控制、品質防禦以及機器人控制等。台積電的製程管制和分析系統不只可以自我診斷和自我反應,還具備自我學習的能力。
未完,請打開下半篇【台積電數位轉型的下一步,靠AI推動全面轉型(下)】
更多【台積電全面AI數位轉型大解密】封面故事內容
【獨家披露】台積電數位轉型的下一步,靠AI推動全面轉型(上)
【獨家披露】台積電數位轉型的下一步,靠AI推動全面轉型(下)
【獨家披露】【加速數位轉型5大發展】台積電為何大動作招募這3類全球IT人才
【獨家披露】台積電30年IT和AI發展史(1996~2020和未來)