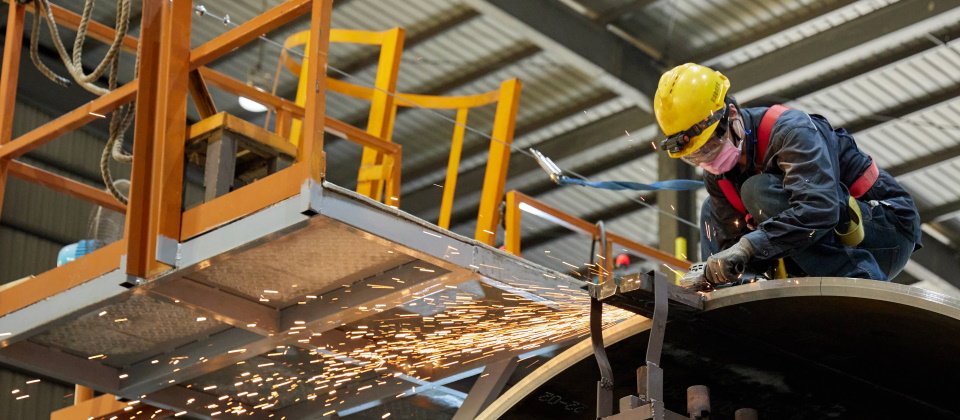
這兩年,一場電光火石般的IT數位轉型,正在新光鋼鐵集團悄悄地展開中。
就在地處偏遠的彰濱工業區附近,一座15,000坪大的鋼鐵廠中,有一間專門生產風電設備的新型廠房,新光鋼IT轉型先從這裡開始展開。
由新光鋼APEX團隊打頭陣,僅用不到半年時間,就完成產線關鍵流程數位化。老字號鋼廠開始改變,甚至還擁抱IT現代化的敏捷思維,加速流程優化,連20公尺超大單圓長管的生產過程,都要數位化、行動化,邁向工業4.0的數位智慧化轉變。
走進廠房,轟隆隆的機械運轉聲和熱風馬上迎面而來,入口處堆滿一片片大型鋼板,正要準備送到裡面進行焊接加工,一旁老師傅加緊趕工,製程一站接一站,把一支支長達20公尺的鋼製長管組裝起來,準備送交客戶手上。這些長管是離岸風電水下基礎設施很重要的關鍵基座。這些生產流程、關鍵製程,正一步步改變,要更敏捷,更有彈性。
這不僅僅是傳統重工業的IT轉型,更是新光鋼一次很重要IT實驗,希望把這次成功的IT轉型經驗,快速複製到全集團,為這家已經快一甲子的老牌鋼鐵製造商,敲響IT轉型的關鍵一步,讓這頭傳產大象也能跳舞。
老牌鋼鐵廠跨出變革的第一步
這一場變革,從約莫2年多前開始推展,「我們從數據蒐集開始,踏出集團數位轉型第一步,而APEX就是新光鋼IT轉型第一個重要實驗場。」新光鋼鐵財會副總經理暨資訊長劉百慧表示。
身為臺灣老字號鋼鐵製造商,每年有超過40萬噸的鋼製品銷售,都是出自這家公司之手,小到家具、機械零件、汽機車板金,大到高樓建築、橋樑工程鋼材都一手包辦。它的工廠更遍及北中南,服務超過2千家客戶。
多年下來,不只橫跨多產業,新光鋼近幾年的經營策略出現轉變,從過去鋼鐵買賣轉型朝價值鏈來整合,更在2017~18年大力布局太陽能、離岸風電等綠能商機,從原先熟悉的鋼鐵業,切入到截然不同的製造新領域來發展。這是新光鋼以前所沒有的新嘗試,不只重砸10多億元建新廠,還因此成立一家前端離岸風電設備製造公司,也就是APEX,投入離岸風電設備製造。
為了要應付全新的產線和新機臺設備,APEX也經過一段時間摸索,APEX總經理黃俊傑回憶,光是前期討論和分析及找到對應製程機臺,就花了數個月,之後更花了一年多完成廠房、設備進註。這段期間,他們也派人到國外學習歐洲焊接工藝、新工法、新設備操作模式並帶回臺灣,「我們用了一年多時間練功,一直到2019年準備好了。」
工廠剛啟用時,除了要一邊接新訂單,還要不斷改生產方法,縮短學習曲線,黃俊傑也帶領APEX團隊一邊學習持續累積經驗,應對新工廠和設備全新的生產流程和作業模式。一段時間後,先從冷鋼板加工生產開始,接下來焊接製程也跟著上線。
在生產過程中,這間鋼鐵廠對生產數據記錄和管理有很高要求,因為他們所要面對終端顧客,大多是如歐洲等國際客戶,和過去以內銷市場為主的新光鋼很不一樣,這些顧客更重視製程數據呈現,尤其這家公司的產品又是離岸風電水下關鍵基礎一環,對於成品品質的要求更高,甚至得做到百分百的品質。像是在焊接製程中,就要求要做到百分百的全檢,把所有中間可能產生的一些瑕疵問題、原因,逐一抓出來,加以解決,來確保百分百的產品品質。
為了要符合離岸風電相關歐盟與客戶要求,產品生產過程必須保留完整的可追溯性,所以他們一開始就建立一套完整的生產表單,詳細記錄每個生產的環節,從板材編號、焊材批號、焊工編號、量規儀器編號、加工及檢驗日期等,皆有留下完整且詳細的記錄,可供作日後稽核的參考。
就像其他新光鋼工廠一樣,APEX成立初期並沒有在工廠導入IT數位化,而是大量依賴傳統紙本作業,來記錄每個生產的環節,從進料、加工到出貨都是如此,需要使用大量紙張來記錄,平均生產一個產品,可能就會用掉170多張的A4紙,所以常常看見現場作業人員,手提著一本本厚重的生產履歷、量測履歷,在工廠內穿梭。
一開始數據蒐集方式、記錄方式,仍然維持紙本的原因,黃俊傑解釋,若是IT太早進場,導入無紙化系統同時,還要一邊設計表單,每個顧客的表單或ISO文件的表單製程的完整性都是問題,很難在系統導入過程中一次就能把所有表單轉換成無紙化文件,一旦表單不完整,現場人員填寫準確度不夠,把這個習慣帶進作業現場,這個無紙化環境就可能會失敗。
所以APEX採取的策略是,先用原本紙本所熟悉的作業方式,等到整套作業流程、完整的紙本記錄都確定完,每個工站都有各自表單文件後,才開始準備e化,將紙張環境轉成無紙化環境,也把以前使用的產品履歷文件轉成電子化的產品履歷文件,「當產品有達到一定品質,客戶認為你的產品是可靠,之後對系統化產生的數據,就會產生信任,這樣就不會失敗。」黃俊傑說。
新光鋼轉型第一站,從離岸風電製造的工廠數位化流程做起
經過一段時間發展,直到2020年,APEX開始展開轉型,也因為過去這段很紮實的紙本流程的建立,之後在建立工廠數位化流程時,就能很快把紙本表單,全部轉成無紙化表單。
劉百慧表示,從APEX開始推動轉型的原因,一來是團隊成員相對年輕,對新科技的接受度較高,也較能發揮團隊凝聚力;二來因為是新啟用的廠房和新機臺,更能支援資訊化作業,加上所面對的終端顧客,很重視製程數據呈現,「長遠來看,電子化的推行成功,可以幫助這家公司做好生產接單,更能取信於客戶。」
成軍短短幾年的APEX,更肩負了新光鋼一個重要的數位轉型實驗計畫,他們的第一個改造計畫,就是從離岸風電製造的工廠數位化流程,展開這家老牌鋼鐵廠變革的第一步。
一開始數位化轉型規畫階段,APEX也找來了顧問公司LeadBest協助他們做轉型規畫,更擬定未來5~10年的數位化轉型策略。根據他們的規畫,2021~2022年是轉型第一階段,要發展數位資訊化,在工廠導入數位資訊系統,將紙本數位化後,利用數位工具來管理、儲存,累積工廠數據及資產,接下來,將用另外2年時間,也就是從2023~2024年進一步結合數位工具與既有的流程控管、工作模式、商品服務等,達成數位最佳化,這是第二階段。
最後第三階段,則要從2025年開始打造一座數位智慧化的工廠,導入生產品質管理、生產履歷管理、出入庫追蹤智慧管理、人員管理智慧排程、瑕疵與故障報告智慧化等。
在流程數位化的過程中,APEX不是一次做完所有流程數位化的改造,而是先從關鍵的產線流程改造做起,先挑了其中的焊接流程來進行數位化。這是因為對鋼鐵業來說,焊接是所有生產過程中最需要資料蒐集,而且是最難的製程環節,所以先從這段流程的數位化改造開始做起。
一般來說,鋼鐵加工有很多製程,以APEX生產的風電水下基樁來說,因為要把鋼板製作成長管,其中切割就是一個製程,捲起來是另一個製程,鋼板捲成圓要做焊接,焊接又有三道製程,每道製程都是1~2臺的機臺,捲出一個柱子的圓柱後,還要把多個圓柱串起來,變成一支長管,這又是另一個製程。目前APEX在工廠的焊接、鋼板驗收的環節,已經完成流程數位化,還搭配行動平板一起來使用。其它製程流程數位化也正進行中。
流程數位化的目的,是要取得更完整、更即時生產數據,有了這些數據之後,後續就可以做更好地的運用,讓數據可以發揮更大價值。黃俊傑就表示,這些數據本身,除了可以維持生產參數的穩定,以後也能用來改善工廠生產效率,或優化製程,長期累積下來,這些數據也將變成APEX自己的資料庫,可以作為訓練資料供員工學習。不僅如此,對於生產流程、製造過程中產生的數據,未來還能夠用於行銷,例如透過數據分析,幫助公司找出適合產品的市場定位或定價。
從數據管理角度來說,劉百慧提到說,過去紙本作業會大大影響到後來用數據管理的方式,因為早期沒有記錄數字,完全由人工來決定數字要不要揭露,現在許多工廠機器後臺都是由電腦管控,所以,她的期待是:「讓數據直接說話,讓機器說自己的故事,員工就可引用有故事的數據,而不是停留在數據蒐集處理,這是新光鋼導入電腦化、系統化的重要原因。」
新光鋼鐵財會副總經理暨資訊長劉百慧表示,新光鋼鐵集團從數據蒐集開始,踏出集團數位轉型第一步,而旗下子公司APEX就是新光鋼IT轉型第一個重要實驗場。
2年Scrum實踐經驗,加快工廠往全數位化流程來推進
在這一段新系統開發之旅,團隊的敏捷力,成了新光鋼數位轉型的另一股重要推力。
從2020年底,進到系統開發階段,APEX的開發作法開始跟新光鋼母公司的做法不同,除了原本委外一組開發團隊,也讓所有現場執行單位、營運單位,都同時來參與開發。
APEX從一開始更導入Scrum敏捷開發作法,來進行數位化系統的開發,還建立自己的Scrum開發團隊,成員由委外開發團隊和APEX團隊組成,以每兩周一次產品或功能交付的方式快速迭代,「時間這個速度是我最重視的」劉百慧指出,透過引導和持續不斷回饋,讓現場執行單位可以用說故事方式,表達自己的需求,再交由開發團隊來開發,透過每一次快速產品功能交付和意見回饋,讓開發出來的系統或功能,也能夠更貼近現場使用單位的需求。這個混合的Scrum團隊到現在已經有2年實踐經驗。
以Scrum開發方式進行半年後,APEX已經在工廠完成不少重要流程的數位化改造,以及新系統建置,如生產管理系統等,加速整個e化的進程,並也獲得了初步成果,包括降低70%的紙本作業成本,提升了50%的行政流程效率,生產流程e化比例達到9成,接下來,將持續優化生產管理平臺,累積生產數據,還要打造數位化的戰情中心,以及結合數據分析工具,來打造更數位化、更即時、智慧化工廠營運模式。
這場IT轉型實驗,成了未來新光鋼集團人才的孵育場
除了技術導入以外,全員參與或透過敏捷方式,另外一個很重要的意義是,讓所有人可以共同學習,不只學習自家的專業,還可以跨到不同領域或環節來學習,可以訓練一個更通才或跨領域、跨流程的團隊,這些可以透過敏捷實現,這些參與的成員,最後都會變成種子人員,一旦要建新廠,就可以將這些經驗複製過去,劉百慧明白表示:「這場IT轉型實驗,對於人才培訓、能力養成也是一個新光鋼集團嶄新的實驗,更是未來集團人才的孵育場。」
有了這次轉型成功經驗,劉百慧也說,以後要導進到新光鋼集團,先前這些成功案例的IT改造經驗,就會起到一個很好的示範作用,除了讓老員工比較有信心,不怕轉變,也更有故事的張力和說服力,讓集團其他工廠願意配合來轉型,「當我們跨出這一步,集團才有可能改變。」
為何焊接流程e化,會這麼關鍵?
新光鋼APEX展開工廠數位化第一步,先從焊接流程數位化開始做起。為何焊接流程e化,對於鋼鐵業來說,會如此關鍵?前端離岸風電設備製造(APEX)總經理黃俊傑直言:「因為數據對於焊接品質很重要。」
尤其,APEX工廠主要加工生產的是風力發電在海底下的基座,對於焊接品質的要求,遠比一般鋼鐵製品更高,例如,焊接條件必須能夠承受負40度的超低溫測試,來確保長管焊道沒有脆裂,甚至焊接過程中只要有一點瑕疵都不行,如氣孔或出現雜質,就有可能在彎曲測試時造成破裂情形。又如海上打樁作業時也要預防焊道或對接處的地方是沒有任何瑕疵,一旦出現瑕疵,日後也很難修補,不然就得耗費很高的成本。
所以如何從前面製程一開始,就把所有焊接品質做到很完整,來減少日後海上基礎維護次數,數據取得就很關鍵。
黃俊傑表示,焊接條件最重要的還是科學根據,就是電壓、電流、速度及入熱量,當入熱量太高,鋼鐵很有可能產生脆裂,入熱量太低又可能熔合不了,所以所謂的焊接條件是有它的科學依據,多少溫度、電流,以及使用多高預熱溫度,產生出來的焊道品質,就是一個範圍內的科學根據。
以歐洲為例,在做這些焊接時,一開始都會先進行焊接測試,來讀取設備上的電壓、電流和速度,來確保入熱量,以及最後的機械性質是在合理範圍而且是合格的成品,這就是一個標準的焊接參數。
所以在還沒有生產產品前,工廠就要對自己產線的焊接設備進行測試,來驗證這個產線組裝完之後種種條件產生的性質。一開始就要先蒐集一套預先產線的設備標準數據。
即使如此,工廠用的每套設備,會因為使用的設備種類不同,輸出功率又不一樣,所以需要的焊接條件、焊接程序規範(WPS)也有所差異,只可運用在這個工廠,到另一個工廠,遇到新的環境,還是必須重設不同焊接條件,甚至很多環境因素,都會影響到焊接條件,所以才說,焊接是鋼鐵加工過程中,最需要依賴數據的一個環節。
完成焊接流程數位化後,往後對於數據取得和分析也將更容易,能幫助工廠進一步找到最佳的焊接組合配方。
熱門新聞
2025-03-03
2025-03-03
2025-03-03
2025-03-05
2025-03-04