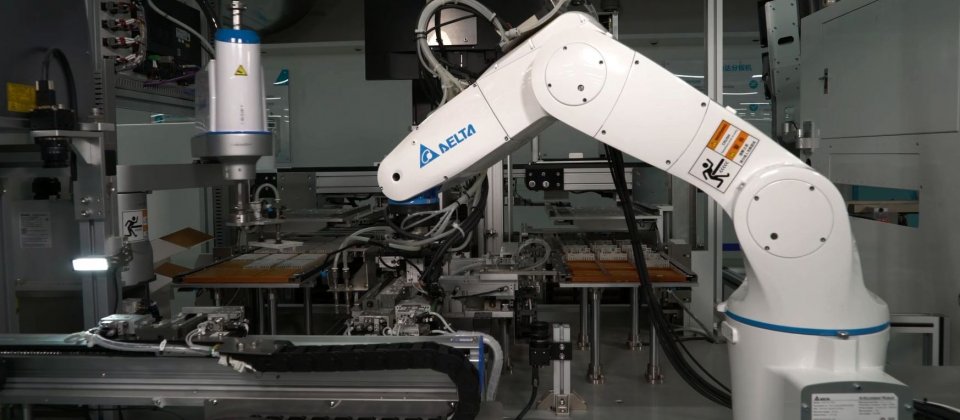
台達提供
台達與微軟、遠傳電信、PTC合作,在桃園龜山工業區一間工廠導入5G專網,建立5G示範產線,以5G的高速傳輸、低延遲,結合自動插件機、 AGV、AMR及AR示範智慧化生產環境。
去年國內邁入5G時代,遠傳、台達電、微軟、PTC便對外宣布將聯手建立5G智慧工廠示範,今天台達電終於對外展示合作成果,位於桃園龜山廠區的5G專網示範產線,讓外界一窺5G如何提升智慧製造。
台達總裁兼營運長張訓海表示,自動化在製造業已推行很久,然而,過去的自動化是大量生產的自動化,現在及未來的自動化,是多種少量、彈性化生產的自動化,是製造業夢寐以求的,但大量的自動化容易實現,而少量多樣的自動化卻是困難的,以一天換線超過十次為例,每次換線若花費半小時到一小時,就會浪費相當多的時間,是非常不經濟的,也是少量多樣較難以做到自動化生產的原因。另方面,過去全球製造是集中生產,未來製造是分散生產,移到市場所在地生產,就需要智慧化、彈性生產線。
此外,由於生產自動化需要連線,才能作精密控制,過去是以有線為主,因為無線不可靠,無法即時上傳資訊作精密控制,張訓海指出,5G的出現改變情勢,不只是固定式的機臺,移動式的機臺也能連線,過去AGV為固定式,現在可以搭載機械手臂,隨產線調整移動,做到過去不能做的,都需要無線來處理,加上VR、AR的人機協作,提供遠距教學、機器維修、送料,AIoT加上邊緣運算、5G能容易建構智慧化工廠。
台達從1995年開始推動自動化,2017年就開始推動轉型,朝智慧化製造發展,在全球超過20個廠區陸續進行產線的汰換升級。台達也說明該公司的智慧製造六大關鍵概念,簡單化與合理化(Simplify)、標準化(Standardize)、模組化(Modularize)、數位化(Digitalize)、虛擬化(Virtualize)、自動化(Roboticise),以簡單化與合理化作為智慧製造的基礎,避免自動化設備的設計過於複雜,以標準化、模組化研發各種軟硬體,有系統的開發之下,可重覆再利用,省下重覆開發,數位化、虛擬化則能降低實體測試的次數,降低成本。
今天展示的5G智慧工廠,為位於桃園龜山工業區一間變頻器製造工廠,主要生產工業用向量控制變頻器,台達和三家合作夥伴,在工廠內一條產線導入使用3.5GHz頻段的5G專網,建立一條5G示範產線。台達指出,經過三個月上線實測後,這條產線人均產值提升近7成,產線產值初期提升75%,該公司預估一年內可回收投資,並提升製造競爭力。
為了監控設備、營運管理,台達在工廠設置智慧製造戰情中心,他們利用5G的大規模物聯網連線,蒐集各產線生產設備、管理及營運數據,供管理者在遠端掌握資訊,調整決策。
另外,因應少量多樣、產線換線頻繁,以Azure雲端平臺為基礎,結合生產環境的AIoT,搭配微軟Hololens及PTC的Vuforia,台達將MR混合實境、AR擴增實境用在倉儲備料、產線組裝、設備維護、生產線稽查,例如在倉儲管理上,以MR引導工作人員倉儲路線、料架位置,以縮短入庫及備料的時間;在產線上,引導作業人員操作程序、稽查產線,生產線上設備也能利用MR,提供遠端的設備維護協助。
作業人員依照Hololens的指引,到指定的貨架儲存物料:
戴上Hololens,可以瞭解產線上每個機臺的運作情形:
運用AR進行設備的維護:
以Hololens的產線運用為例,根據現場的解說,作業人員戴上Hololens後,通過虹膜驗證,確認產線人員身分後,再載入對應的步驟指引。在實際的產線作業區上方也設置攝影鏡頭,偵測組裝程序是否有異常,一旦發現程序錯誤即暫停組裝流程。
在自動化生產上,示範產線運用他們自行研發的自動插件機(Rapid Transformable Machine,RTM)取代人工插件,提高產線的自動化,自動判別組裝需要的料件,結合5G網路,加速治具的更換,提升產能。
在這條示範產線上,AGV無人搬運車不時往來於產線之間,代替傳統作業人員的人工搬運作業,目的在提升效率:
在智慧工廠內,也利用5G的高速傳輸,讓AMR自主移動機器人搭配機械手臂,能自動偵測環境、即時控制,讓AMR在設定的區域空間自主移動。
台達並沒有透露5G專網建置成本,而此次和遠傳、微軟、PTC合作為示範性的專案,未來需要評估以決定是否擴大產線,在更多產線上導入5G。該公司表示,導入5G在生產環境的效益,除了讓過去定點使用的機械手臂,未來可透過AMR彈性移動,另方面因為採用5G專網,相較Wi-Fi較為安全,且因為智慧化工廠需要大量視覺化資訊,大容量頻寬5G可滿足需求。