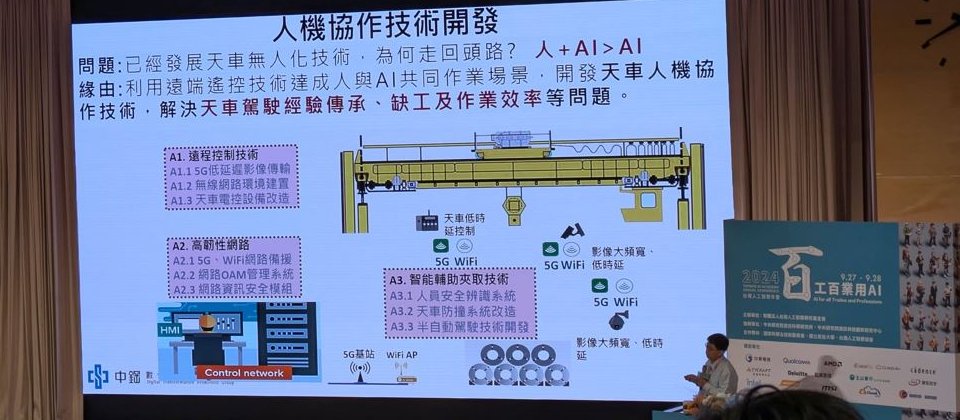
攝影/余至浩
國內生育率低落,產業面臨少子化缺工問題如何解決?老牌鋼鐵業者在新興AI浪潮下如何推動數位轉型,中鋼近期分享如何運用AI加速數位轉型,並提出4大對策,包括研發人機協作技術,運用數位雙生及生成式AI等技術,來克服缺工、經驗難以傳承的挑戰。
中鋼綠能與系統整合研發處研究員許朝詠表示,中鋼約從2014年開始導入AI,主要應用在產線、銷售端,然而儘管中鋼投入大量資源研發AI應用,並且實際落地使用,但卻發現這些AI技術很難為企業帶來明顯效益,因為企業發展AI多是以單一技術或單一產線為目標,以中鋼研發無人天車為例,目標是讓無人天車技術得以實現,但並不容易可以量化,難以呈現為公司帶來的效益。
因此,2023年他們轉換方向,推動數位轉型不僅要讓AI技術能夠落地,而且不論是報表或是整體的營運績效上,最終要帶來實際效益。中鋼成立的數位轉型推動小組,前身為智能產銷委員會,目的是在生產及銷售兩個部門推動AI技術,研發部門則提供生產及銷售部門必要的技術支援。
去年成立的中鋼數位轉型推動小組,他們將資訊及行政部門納入,其中資訊部門負責資訊流的串接整合,行政部門則負責數位轉型的教育訓練及管理,AI核心技術訓練、數位賦能等等。
中鋼委託工研院以全球7大鋼廠為對象,歸納鋼鐵業者數位轉型的4大目標方向,提升生產效率、低碳化製造、智慧化營運、投資新產品,這些目標與中鋼推動數位轉型的目標不謀而合。
如同其他產業在營運上所面臨的困境,鋼鐵業也受到少子化勞力短缺衝擊,並且面臨台積電等科技業者競爭人才,「對於中鋼而言,過去在南部招募人力並不是問題,現在招募人才除了要和同業競爭,還要和科技業競爭,過去聽到的是台積電要來了,現在最常聽到的是同仁要去台積電了」,許朝詠說。
勞力短缺不只影響生產力,對員工高齡化的中鋼而言,人才招募不易,新血來不及補充,年輕的員工愈來愈少,衍生出經驗傳承難題,老員工的經驗難以交給新員工。
4大對策克服缺工難題
「中鋼導入數位技術的整體目標就是,達到2大目標,提升工作效率、加速經驗傳承」,許朝詠說。中鋼提出4大對策,包括提升人機協作程度、提升AI導入效率、建立高效訓練模式、提升經驗擴散速度。
中鋼導入不同的數位技術來實現2大目標,例如提升人機協作程度,結合AI電腦視覺、遠端控制、低延遲通訊技術,讓人員可以在安全的環境下操控設備;基礎建設方面,導入混合雲架構,讓AI應用能在雲地協作式開發、維運,加速推動AI普及;導入數位雙生技術,以數位模擬真實的生產環境,以瞭解虛擬環境的變數對真實世界產生影響;運用生成式AI開發行政、操作、維護各方面的數位助理。
開發天車人機協作技術、遠端協作技術
在鋼鐵的生產環境中,不論原料或半成品,重量多達數噸,一般機械手臂難以搬運,因此中鋼多仰賴天車吊運物料,約有一千多部不同的天車,用於搬運不同的物料及設備,每天天車吊運作業成為鋼鐵產線的重要工作。
為了提高人機協作方面,過去仰賴人工上下天車,在駕駛艙操控天車吊運物料,天車位於廠房的高架上,駕駛操控的天車手因吃飯、上廁所,經常需要上下天車,現場作業環境也有工安疑慮,為了推動自動化,幾年前中鋼研發AI無人天車,不需人工駕駛,讓天車透過電腦視覺及雷射測距,判定需要吊運的鋼捲位置,自動化吊運鋼捲作業。
但是,由於AI難以完成細緻化的吊運作業,因此天車雖為三軸同動,中鋼僅在限制環境下讓AI操作天車,例如AI無人天車只能兩軸同動,無法執行三軸同動作更細緻化的操作,即使無人天車能夠24小時作業,難以完全取代人力。
因此在無人天車之後,中鋼也開發天車的人機協作技術,他們在天車作業環境部署5G及Wi-Fi,並建立 5G及Wi-Fi網路備援,滿足天車遠端控制的低時延通訊需求,搭配大頻寬傳輸天車作業的即時影像,開發智能輔助夾取技術,包括改造天車防撞系統、人員安全辨識系統、天車半自動駕駛技術。
以小鋼胚的天車吊運作業為例,傳統上,天車手和地面人員協作,天車手操作電磁吸盤吊運多個鋼胚,從A儲位吊運到B儲位,每次吊運的鋼胚數量由地面人員計算後,輸入到倉儲管理系統(WMS)。
為克服缺工問題,中鋼在天車吊臂上架設攝影機,利用AI電腦視覺辨識天車所吊運的小鋼胚數量,然而,他們很快發現儲位大量的鋼胚,導致AI辨識吊運鋼胚數量容量誤判,因此他們在攝影機旁邊再加裝雷射線,每次天車吊起多個鋼胚,將雷射線打在被吊起的鋼胚上,由AI偵測雷射線區分被吊起的鋼胚和儲位的其他鋼胚,自動計算吊起的小鋼胚數量,利用這個方式,在天車多次吊運測試下,AI計算鋼胚數量的正確率提高到99%。
許朝詠表示,AI落地經常發生的問題大多和環境有關,他認為AI專案應用有3個層次,第一個層次是單純使用AI技術,因為條件不可控,使得AI技術難以符合現場環境;第二個層次是限定環境使用AI,以天車吊運鋼胚為例,使用雷射線即是限定環境使用AI技術,但是容易因為環境變異造成AI辨識失準;第三個是精確設計環境後使用AI技術,控制雷射線只打在吊起的鋼胚上,在設計的環境中就能很好地使用AI技術。
另外,中鋼也開發天車遠端協作技術,在第二熱軋鋼帶工廠,利用5G專網涵蓋鋼捲儲區,透過5G網路及Wi-Fi網路備援,建立低延遲網路來傳送控制命令,同時改造天車系統,將控制訊號拉到控制室,使其可以遠端控制,天車手不需登上高處的天車,只要在地面上安全的操作臺,透過多個螢幕呈現不同視角的天車操作即時影像,從遠端操控天車吊運鋼捲。
如圖所示,天車手只需在地面控制臺,透過多個螢幕來遠端操控天車吊運鋼材:
天車手在地面的控制臺遠端操控天車,中鋼也盤點天車吊運鋼捲作業程序,評估比較各個程序由人工或AI操作差異,他們發現吊取鋼捲、放置鋼捲比較適合人工遠端操控,其他如電子圍籬、防撞系統、鋼捲號碼辨識、點到點移動控制等程序則可由AI代勞,如此一來,每個天車的人工操作負擔大幅降低。
許朝詠表示,原本的人工操控天車程序,在導入人機協作後,人工操控只剩下夾取、放置鋼捲,其他則由AI自動化控制,天車手的工作負擔降到原本的20%,天車手剩餘時間可以切換操控其他天車,未來一個人可以遠端操控多臺天車,提高工作效率。
運用數位雙生技術模擬天車操控、高爐內佈料情形
為了訓練新手操控天車,中鋼打造模擬訓練系統,利用數位雙生技術打造鋼捲倉庫的數位分身,天車新手可以先在鋼捲倉庫的模擬環境中,練習操控天車吊運鋼捲,這套訓練系統支援駕駛艙操控及遠端遙控操作,讓天車手考照的同時,先熟悉未來的工作環境。
在鋼鐵的生產過程中,高爐用於高溫熔煉原料產生鐵水,但是高爐內上千度高溫,高爐內操控在鋼鐵業的產線過程中如同盲盒,高爐內布料的情形不易被瞭解,中鋼運用數位雙生技術打造高爐的數位分身,
許朝詠指出,中鋼透過Nvidia Omniverse建立高爐佈料的模擬,模擬高爐爐頂佈料到料面的情況,瞭解和真實高爐的佈料情況是否一致,從模擬系統的佈料變動,預測判斷真實高爐佈料的結果。
以生成式AI打造數位助理,加速經驗傳承、職能訓練
為了加速新舊員工的經驗傳承,以及新手員工的訓練,中鋼也運用生成式AI,以多年累積的既有知識庫結合ChatGPT,開發個人的數位助理。以生成式AI數位賦能員工,將他們不具備的技能、知識,讓他們具備或是能夠從系統中提取。
許朝詠認為讓員工大量使用生成式AI,最終他們會從工作場域中找出合適的生成式AI應用,並且提出他們的需求。
目前中鋼內部已有生成式AI應用,例如將設備、線路資料格式化後存於資料庫,傳統上,不會SQL語法的員工需要仰賴熟悉SQL語法的其他人協助,從資料庫中取得需要的資料,現在利用生成式AI,不會SQL語法的員工得以自然語言提出問題,由AI生成SQL語法從資料庫中取得資料,再以自然語言回答。
中鋼運用生成式AI開發工程小管家,工程人員遇到問題,可以自然語言向系統提問,由小管家搜尋資料後回覆:
另一個生成式AI的應用實例是在維修指引方面,資深員工多年從事維修工作所留下的文件,中鋼根據這些文件開發維護指引系統,結合生成式AI,維護人員遇到不熟悉的維護難題,可以自然語言向指引系統提問,由指引系統找尋資料答覆,讓新手員工學習如何維護設備。
許朝詠指出,數位轉型過程中最重要的是,如何導入數位技術協助員工完成工作,中鋼在推動數位轉型中導入各種數位技術,例如導入AI來開發遠端操作人機協作,利用人工和AI各自的優點打造人機共同作業,以提升工作效率,其次是導入數位雙生技術,在建立數位分身的過程,藉此機會盤點內部的資訊流是否足以呈現實境情況,以及虛境模型能不能解釋實境的現象,「能夠做到這兩件事,數位雙生才能帶來效益」。另外,中鋼導入混合雲,結合低程式碼工具,讓員工可以快速建立AI應用,最後運用生成式AI建立專家詢問系統,活用過去員工的經驗資料,讓新進員工汲取知識,獲得經驗傳承,達到訓練效果。
更正啟示:文中提及中鋼委託單位研究全球7大鋼廠數位轉型策略,誤植研究單位,內容已作更正。
熱門新聞
2025-03-03
2025-03-03
2025-03-01
2025-03-03
2025-03-03
2025-02-27