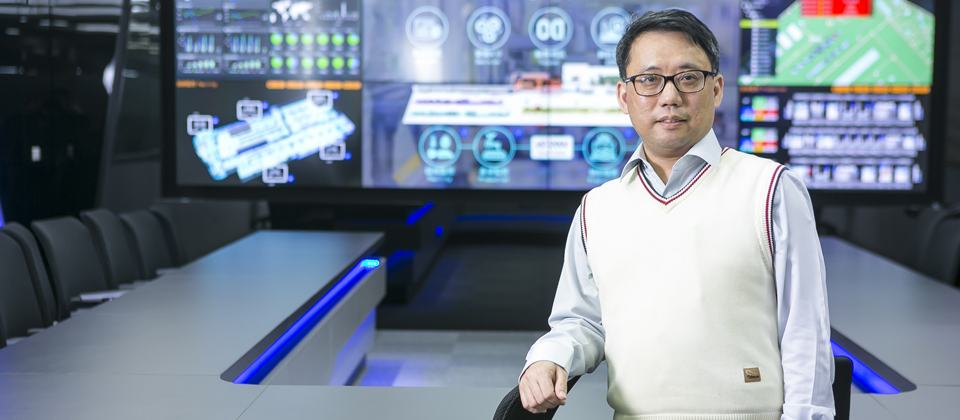
新漢資訊處處長姚達威
儘管設立超過20年,工業電腦硬體商新漢近年不斷力求突破,去年底,更啟用了首座工業4.0智慧工廠,大步朝智慧化生產邁進。為打造這座近3千坪,落腳在桃園華亞科技園區內的智慧工廠(簡稱華亞廠),新漢大砸2億元,購置軟硬體設備,而這座工廠從去年3月開始建置,6月展開試行,10月便正式啟用,投入生產。
「數位轉型,無法一步到位。」新漢資訊處處長姚達威直言。要從無到有,打造一座智慧工廠,不是一件容易的事。新漢花了至少7年時間,著手為數位轉型鋪路,才能發展智慧化製造。新漢在華亞廠內,導入自動化設備,整合工廠生產與營運資訊,並建置自動化雲端戰情中心,才成就了工業4.0的示範工廠,而新漢之所以能在短短3個月內,讓一切到位,IT扮演了至關重要的角色。
過去單純生產工業電腦的新漢,近年面臨PC廠商進入市場,分食大餅的競爭壓力,因此新漢的毛利率逐年下滑。面對強勁的威脅,新漢從2012年開始,為了走出代工模式,建立自有品牌,陸續成立了智能監控事業部、醫療資訊事業部,並將工業電腦事業部改名為IoT智動化事業群,開始切入多個垂直應用領域。花了7年,才打造出了現在的智慧工廠,讓新漢擺脫了傳統的代工廠角色,轉身成為了提供解決方案的服務商。
不同於舊有的板橋廠,華亞廠全面導入自動化生產機臺,從料件撿出、電路元件打件、DIP插件,到硬體組裝、檢測及產品裝箱,改用機器取代了傳統人工作業,只需原工廠一半的人力,來處理難以自動化的目檢、手插件等作業,連帶也提高了生產效率。
雖然,姚達威今年初才接任處長,不過,他一路參與智慧工廠的建置工程,且上任後,他除了要維護新漢既有的營運,更要支撐新漢朝智慧工廠發展,整合IT與OT的資訊。建置智慧工廠後,新漢的數位轉型之路仍有許多難題,需要IT一一克服。
一般工廠在朝智慧製造邁進時,都會從翻新系統開始著手,不管是翻新支撐維運的ERP系統,或是升級管理產線的MES系統,然而,新漢並沒有這麼做,而是直接改造既有系統來符合新的需求,姚達威解釋,因為IT只有3個月的建置時間,為了避免維運人員及工廠作業員重新適應系統,不大動作翻新既有系統,而是改用介接方式來增加新功能,例如整合機臺資料。
除了時間壓力,也因新漢原有工廠早在2008年就導入MES系統,過去10年,為因應產線的需求,陸陸續續在MES系統上客製了許多功能,為此,這些客製功能必須重新修改程式,才能在新系統上執行,同樣非常耗時,這是新漢選擇沿用既有MES系統的另一關鍵原因。
雖然節省了翻新系統所需消耗的心力和時間,但姚達威直言,直接在舊系統上擴充的最大挑戰是,須遷就舊系統的架構,因而面臨了許多限制。像是為了讓ERP系統和MES系統,能與產線機臺間交換資料,新漢必須整合雙邊系統,然而,系統與機臺的介接方式不一致,而各機臺各自有不同的介接方式,如何協調系統與機臺間的介接方式,成為IT最大的挑戰之一。
機臺串連MES及ERP,IT必須出面協調各廠商的介接方式
![]() |
新漢資訊處處長姚達威表示,跨系統整合,不僅要考慮串接方式,更要全面評估串接後的影響,IT出面協調是關鍵。攝影/洪政偉 |
改造工程的第一步,IT先評估系統使用者提出的需求,再召集廠商一同討論介接的規格,姚達威表示,不僅要考慮系統串接方式,更要評估串接後會帶來的影響,他強調,必須全面性衡量,因任何一個介接機臺若發生問題,將影響整個產線的運行,「協調是關鍵。」
他回想整合過程,花了不少時間,反覆地召集各家廠商,甚至有時需一次聚集5家廠商一同討論,花了近兩個月的時間,新漢才與各廠商完成各項系統間的介接。
如此大費周章地將系統與機臺串聯,就是為了背後可帶來的加值運用,讓機臺能從系統中,對應到該款生產品的資訊,從而執行任務,以發揮自動機臺的生產效益,姚達威以自動倉儲為例,透過系統串接,自動倉儲從ERP抓取工單中的發料資訊,自動送出產線上SMT打件所需的SMD料捲。
或像是負責雕刻主機板上序號的雷雕機為例,在系統介接後,現在雷雕機可直接從MES系統的工單中,自動拋轉每一張主機板所對應的序號,來自動刻上該主機板。華亞廠內產線中,已有7個機臺,完成與MES或ERP的介接。
另外,新漢還在華亞廠的組裝作業區設置大型螢幕,直接秀出MES系統的生產資訊,包含預期生產數量、目標數量和即時生產數量,以便現場作業人員掌握生產進度。姚達威解釋,相較於ERP系統,MES系統與工廠產線端有最直接的關聯性,若能精準地將資訊傳達到產線中,便可加快產線效率。「每加快一分鐘,即是增加一分鐘的產能,而這正是工廠最關注的事。」他強調。
不過,新漢華亞廠將MES系統與機臺串接後,對系統可靠性的要求也得更高,因此,改直接將MES系統部署於虛擬化伺服器,來降低停機風險,並搭配高可用性的儲存架構,相互備援,而不像過去直接部署在實體主機上的作法。
下一步,姚達威計畫升級MES系統,除了提高靈活度,還能透過外掛機制,彈性擴充功能,最重要的是可自行修改。他格外重視最後這一點,因新漢這一波機臺介接,還是要委託給MES廠商擴充,也衍生了可觀的委外開發費用,他認為,新漢需要提升IT的自主性。
除了打通機臺與MES實現生產流程自動化,針對產線最後一段,也就是組裝作業流程,新漢也做了不少改善來提高效率,例如導入RFID感測器。當生產品通過組裝站時,感測裝置可以自動感應到生產品的RFID標籤讀取序號,再將該項物品的組裝進度直接匯入MES系統,取代原本手持掃描器掃碼的流程,讓作業員專注於人工組裝作業,也因而再進一步縮短了產線作業時間。
華亞廠產線導入RFID,直接在產線實戰測試,邊測邊調整
新漢直到去年9月才完成這套RFID產線系統,距離華亞廠10月正式投產,僅僅相隔1個月,無法另闢產線進行RFID測試,新漢IT只能挑選交期不緊迫的工單,直接在該工單生產線上,進行實戰測試,邊測邊調整。
姚達威回想那段測試期間,每天最多只有2段時間可以測試,一旦RFID系統發生異常狀況時,像是資訊傳遞有誤,若是無法於20分鐘內排除問題,就要直接退出RFID系統,恢復人工作業,否則就會造成產線中斷。經過1個月,遭遇多次難以快速解決的問題,反覆緊急退出重啟測試,IT人員也逐步與廠商協調,才將系統修正到位。
不只優化組裝作業,新漢IT也將RFID應用於輔助生產的治工具管理系統上,姚達威舉例,像是支撐主機板打件的鋼板,現有了RFID標籤,可管控鋼板使用的次數,進而降低打件錯誤率,又或是焊接需要的錫膏,透過RFID,可管控錫膏離開冰箱後,回溫時間的長度,以確保錫膏的溫度,及掌握錫膏投入的工單,以作為日後品質改善時的參考。
其實,早在華亞廠導入RFID標籤前,新漢就於2017年時,在板橋廠導入RFID管理倉儲管理系統(Warehouse Management System,WMS),以便管理半成品倉。新漢將RFID標籤,貼在有固定數量的PCBA板或主機板半成品紙箱上,並把箱中半成品的物料序號與該標籤綁定,當拖車進出倉時,可直接通過感應門,系統自動掃描棧板上所有紙箱的RFID標籤,不再像過去以人力逐條掃碼,姚達威表示,在這個階段,因而大幅減少了9成以上的作業時間。
不只縮短倉儲作業時間,RFID也讓新漢可以落實「先進先出」的標準,確保使用先進倉之物料的半成品,先出倉。半成品入倉後,RFID可以定位存放位置,更可記錄每個半成品所使用料件的序號,從而掌握料件進倉的日期。
過去,新漢靠人力直接依據紙本工單的資訊,進入倉儲撿料,然而,ERP只管控數量,姚達威指出,現場操作員無法從ERP中,獲取料件的進倉日期,所以,倉庫未導入 RFID 前,只以區域大略估算半成品的時間性,撿料時,需靠大量人工及花費大量時間核對,所以每個月仍平均有4到5件錯誤,但現在錯誤數則降為0件。而且,當時新漢板橋廠導入RFID,便是為智慧工廠的建置做準備,屬於實驗性質,所以,華亞廠成立時,新漢也同步將此RFID倉儲管理方式,帶入了新智慧工廠。
接下來,新漢也計畫擴大RFID在倉儲的應用層面,延伸至管控物料倉和成品倉。相較於半成品倉,這兩種倉儲導入RFID的難度提高了不少。像在物料倉中,物料品項多元,且體積各有不同,每種品項的數量都相當龐大,而成品倉的挑戰是使用版次的複雜度。姚達威解釋,半成品的品項較少,控管相對容易,這也是新漢先從半成品倉開始導入RFID的原因。
為進一步邁向智慧製造,姚達威則計畫升級先進規畫排程系統(APS),來強化ERP欠缺的排程功能。新漢現有的APS只具備了基礎查詢功能,無法規畫工單排程,因此,新漢只能先以無限產能原則來規畫,無法依據現場產能狀況,更動態地調配產線。
系統化排定工單順序,是智慧製造不可缺少的一環
然而,姚達威認為,工單排序自動化和系統化,是智慧製造不可缺少的一環。以先進規畫與排程為原則,快速整合生產資訊,以反映訂單需求數,不以產能為首要考量,而改以需求日為參考標準,將相同產線製造流程的工單,集合在一起生產,才能減少產線的換線次數,不只可降低成本,又能兼顧效率。
新漢於去年啟用華亞智慧工廠後,將新廠的自動化機臺與ERP系統和MES系統相連互通,還在廠內打造了戰情中心,整合ERP與MES的資訊,在大尺寸的螢幕上,可展示9大應用模組,包含工廠製造資訊、預知維護、會統4.0管理決策等,像是以視覺化圖表呈現當月訂單和出貨進度,也可監控SMT和DIP產線設備的運作情況,方便管理者和決策者即時監控及掌握生產資訊。
CIO小檔案
新漢資訊處處長姚達威
學歷:美國明尼蘇達大學電腦科學碩士
經歷:曾任職於致遠會計師事務所(安永前身)的 ERP顧問團隊,以及友訊科技資訊部門,於2017年時,加入新漢資訊處,於同年12月擔任經理一職,推動公司內部各軟硬體系統建置,參與建置新漢首座工業4.0智慧工廠,並於今年初接任處長
公司檔案
新漢
● 成立時間:1992年
● 主要業務:製造工業電腦,及提供工業4.0整體解決方案
● 總部:新北市中和區
● 員工數:900人(臺灣)
● 年營收:66億元
● 董事長:林茂昌
● 總經理:楊建興
資訊部門檔案
● 資訊部門主管職稱:資訊處處長
● 資訊部門主管姓名:姚達威
● 直屬主管:總經理
● 資訊部門人數:21人
● 資訊部門分工:應用系統維護與開發,資訊基礎設施建置
● IT預算:2,000萬元
公司大事記
● 2007年:ERP系統改版
● 2008年:板橋工廠導入MES系統
● 2013年:導入產品生命週期系統,並且升級ERP版本
● 2015年:與客戶間資料交換的系統介面開始採虛擬化
● 2017年:板橋工廠導入 RFID 倉庫管理系統及治具管理系統
● 2018年:桃園華亞智慧工廠成立,導入MES系統且採虛擬化,並將RFID應用於該廠產線及倉庫管理系統, 及建置智慧工廠戰情中心
● 2019年:導入微軟 Office 365,使用雲端電郵,及協同合作功能
熱門新聞
2025-02-08
2025-02-08
2025-02-08
2025-02-08
2025-02-08
2025-02-10
2025-02-08