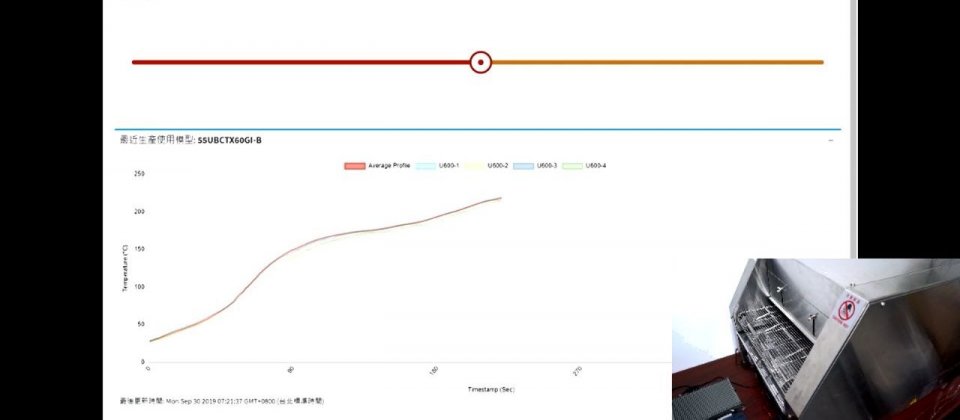
利用在回焊爐內安裝的感測器,即時監控電路板的加溫情形。
科技部/交大資工研究團隊
為加速智慧製造應用在產業落地,科技部推動大數據、AI、物聯網的產學合作,交大資工研究團隊本周發表一項工業物聯網溫控生產預測技術,實際在PCB板的SMT產線上,利用感測器蒐集生產環境溫度,並以AI取代人工憑經驗測溫調校參數,達到100%的生產履歷追蹤,並提升生產品質。
在工業製造的過程中,需要精準的溫控生產程序,但由於生產品質和產品承受的溫度及時間有關,同時涉及多個參數的互動影響,在製造的過程中僅能控制設備的加溫曲線,無法即時掌握環境、設備,以及產品在製程中的受熱情形,傳統上多由人工依據經驗,利用頻繁的量測、校正調整,以控制生產過程確保生產品質,如果要生產新的產品,更需要一段時間摸索,不斷的透過嘗試錯誤去調整製程參數、進行優化,趨向穩定生產。
研究團隊以工業物聯網結合AI,嘗試解決這個問題。交大資工系教授曹孝櫟以「溫故知新」來形容,所謂「溫故」即透過有系統、有結構的蒐集、累積工業大數據,而「知新」則是運用這些資料去推論、預測沒有生產過的物品該如何生產,特別是產品快速迭代之下,如何快速收斂,有辦法穩定的大量製程,「知新」從過去的大量資料,透過AI抽煉出上位知識,再推論到新的產品生產上。
他指出,對於溫度的提供可從兩方向著手,一種是從物理的熱力學來看,熱傳、熱導、熱對流,有很好的定性分析,但缺乏定量結果,另一方向則是數據驅動的定量分析,能夠得到很好的定量結果,但無法解釋很多定性行為。研究計畫運用物理學的方法,得以關鍵、少量安裝感測器,從蒐集的資料推回參數,同時達到定性的解釋性及定量的結果。
曹孝櫟表示,經由感測器可紀錄每個產品的生產過程,能夠做到百分之百的追蹤檢測,建立生產大數據,累積兩三年的數據,透過大數據及AI技術抽煉出上層知識,應用在加速新產品導入,協助工程師快速收斂到能穩定量產的階段,這對於現今少量多樣、產品快速迭代是很重要的。
以PCB板的SMT製程為例,過程中的溫度控制極為關鍵,如果溫度過高可能導致電子零件損壞,而不適當的溫度或加熱速度也可能造成焊接缺陷,降低生產品質,因此,工程師為確保良率,需要為每種產品設計專門的製程參數,並在回焊爐反覆測試。
該團隊在研華協助之下,在SMT產線導入物聯網溫控生產預測技術,在回焊爐內裝置溫度感測器蒐集溫度資料,結合熱力學模型及機器學習模型,建立電路板的溫度預測模型,透過機器學習模擬製程結果、建議參數。利用工業物聯網感測器達到自動化100%監控追蹤製程,解決過去單一的樣品檢測,無法顧及所有產品檢測的問題。
(圖片來源:科技部提供)
曹孝櫟解釋,通過感測器掌握每臺回焊爐的加熱性能,並推論電路板受熱情形,達到100%的檢測及虛擬量測技術,節省停機校驗的人力成本,這是「溫故」的部分。至於「知新」的部分,當產線導入新的電路板,因為已對爐子及電路板的抽象模型掌握度很高,鑑於新產品多為過去經驗及知識的組合,只要將電路板設計檔輸入系統,並輸入使用哪個回焊爐,就能從AI產生出不同加溫效果,協助定出加溫策略,新產品導入生產也能縮短製程參數的摸索過程。
導入這項AIoT溫控生產預測技術後,從輸入新產品資料、產生製程參數,依參數實際測溫,再根據回饋的測溫結果調整製程參數,到最後的產品生產。經過他們的測試,在測溫階段,95%首次測溫合格不需要調整,並有80%的信心指數新產品可直接進行生產。
目前他們已在4家公司、7間工廠、100條SMT產線導入,最長已使用超過40個月, 累積大量數據。估計每年每條產線可減少150個小時無效工時,效益超過5000萬元。
研究團隊研發出兩個系統,並準備推向產業界,一個是回焊爐即時生產品質監控與預測系統,用於即時爐溫監控、完整生產紀錄、生產品質監控等;另一個則是溫控生產新產品參數生成與模擬,用於優化製程參數、模擬生產結果,以及減少產線停機用於新產品生產測試的佔用。
目前將模型的建立、部署、重新訓練、管理在WISE-PaaS上執行,明年準備以App上架至WISE-Marketplace,進一步擴大產業應用。
熱門新聞
2025-02-23
2025-02-21
2025-02-21
2025-02-21
2025-02-19
2025-02-21
2025-02-21