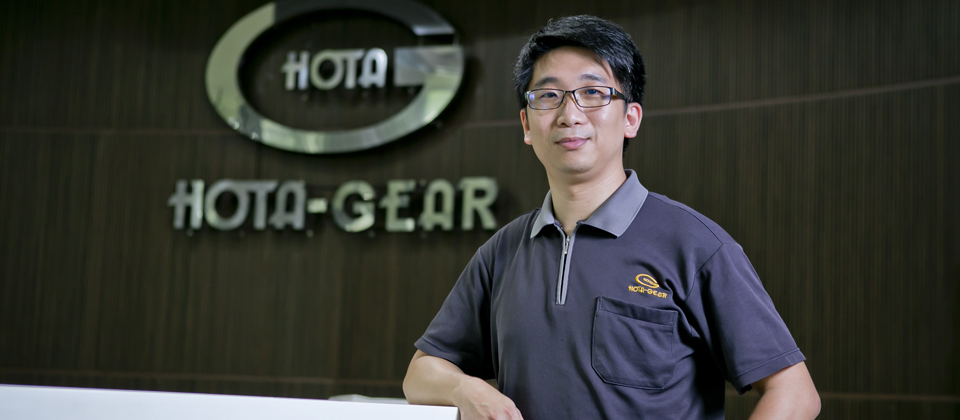
和大工業資訊課襄理 孫水文
特斯拉今年3月平價電動新車款一推出,就吸引全球爆量訂單,一個月就賣出了遠比去年特斯拉整年出貨還要多6倍的量,多達30萬張,連特斯拉執行長Elon Musk自己都料想不到,但負責生產這輛車內關鍵齒輪的和大工業,早在去年就已經開始準備展開布局新一代自動化工廠,還預先利用MES系統蒐集機臺資料來提高產能,以因應大量訂單需求。目前和大新工廠已展開試作,幾個月後,就要上線營運了。
特斯拉已成為和大工業全球第2大客戶
和大工業目前是全球前10大車廠傳動零組件供應商,也是臺灣最大精密齒輪加工龍頭。目前全公司將近有99%的營收都來自外銷代工市場。和大工業資訊課襄理孫水文驕傲地說:「現今,在全球每一輛特斯拉Model S和Model X新車內,用的都是我們生產的減速齒輪。」
和大工業從2012年開始專為特斯拉生產電動車馬達減速用的齒輪零件,至今,特斯拉已躍升成為和大工業全球第2大客戶,每個月光是要出貨給特斯拉的減速齒輪零件數量,就超過了上千個,就連美國三大車廠福特、克萊斯勒與通用汽車都是和大的重要客戶。
但為了因應緊接下來能如期供應這至少30萬張爆量的新車訂單,特斯拉也得要加緊準備才行,不只要大舉投資建造廠房來擴大產能,甚至還得改善整個生產製造流程,盡可能加快提高汽車量產的產能。
不過,做為特斯拉全球關鍵齒輪供應商之一的和大工業,在面對接下來大量增長的代工訂單需求,卻一點也不擔心,因為早在去年,和大工業就已提前布局在嘉義大埔美打造新一代的自動化生產工廠,將原有的加工生產流程,全面改用更快速、更省人力的機械手臂取代,以此做到整個產線一條龍式的全程自動化生產,即使是在面對未來突發性爆量訂單的情況下,也能夠做到正常地如期交貨。
IT團隊去年全力投入新廠自動化IT建置
而早從1年前,孫水文和他的IT團隊便全力投入新工廠自動化IT的建置工作,先是將所有的產線機臺設備和機器手臂全部連網,接著更整合了不同的系統,甚至為了配合今年新廠上線營運時程,孫水文更進一步在今年把公司營運核心的ERP系統升至新版本,可以更緊密地與生產機具做連結。
與此同時,孫水文去年就開始在未完成的新工廠內部,預先導入了一套MES生產製造管理系統,透過持續蒐集產線設備和機器手臂的生產參數與製程資料,做為後續的資料分析使用。
接下來,孫水文更打算結合大數據分析技術,持續改進新廠房的自動化生產流程,以此來調校機臺提高產線產能,也要為公司挖掘出更多的創新價值。
孫水文表示,這座全自動化生產工廠從去年開始動工至今已建置完成,目前也已進入試量產階段,預計今年第3季就會開始上線營運。未來整間工廠總共會有6個產線做為專線加工生產使用,以因應未來大量客戶的訂單需求。
孫水文也透露,就連和大目前位在臺中科學園區內的舊工廠,未來也將逐步全面採用全自動化生產。
不過,和大工業IT並不是一直以來都和工業生產製造流程有密切結合,而是最近幾年才開始出現有的不一樣的改變。
孫水文表示,早期和大工業和其他傳統製造業在IT作法並無不同,不外乎是以ERP和Mail郵件這2個資訊系統最重要。
所以IT人員的平日工作,也都以ERP更新和基本硬體設備維護為主,而較少會與生產製程扯上關係,而生產方面對於資訊系統依賴度也往往不高。這樣的情況,一直到了2008年金融海嘯爆發後才開始有了截然不同的轉變。
和大工業資訊課襄理孫水文說,製造業IT不能只負責硬體,更要站上前線與生產端更緊密地結合。
不再只專做大量少樣訂單,也開始接下更多樣的代工種類
因為受到當時全球金融風爆的影響,和大工業不僅面臨全球汽車市場的重挫,就連當時占有和大全年超過7成營收的美國三大車廠也都瀕臨破產,而得出面請求美國政府疏困,因而促使和大工業只好改變了原有的代工策略,積極拓展新的客源,從以往只專注做大量、少樣的大宗客戶訂單,到後來,也開始逐漸增加了少量但更多樣的加工訂單,如農機具或大型聯結車零組件等。
雖然更多新代工客戶的加入,的確替和大工業短期內改善了營收不佳的問題,但也正因為現在要負責生產的加工零件種類變多了,代工產品也更為多樣,因而也帶來了生產加工品質控管不易這個新難題。
孫水文解釋,通常一個加工產品的完成,過程會需要經過有30~40道加工流程,但在生產期間並非所有加工手續都會在自家工廠內完成,有時,也得靠委外廠商來加工生產。所以,為了嚴格把關每一道加工流程的品質都能合乎標準,就會由品保部門負責檢驗供應商每批送樣的加工零件有無品質問題。
如果只是少部份委外加工的話,品保人員還能應付,但隨著代工的產品種類更多樣,目前和大工業內部有超過5成的加工產品,都需要委外加工的步驟,而無法全部自給生產;再加上,需要合作的加工廠商數量越來越多,檢驗人員平日光是用電話聯繫加工廠商,有時就得占用一整天,更不用說,還要花時間檢驗評估,因而造成品保人員工作上的一大負擔。
更何況,和大工業本身又是以高精密零組件生產為主,當有越來越多加工產品需要委外生產時,一旦加工品質沒有把關好,嚴重的話,不只將會讓和大工業失去原有客戶的信任,甚至還可能讓公司多年累積的信譽毀於一旦。
所以,為了解決這項難題,孫水文便毅然決然地在2012年導入了一個供應商訊息服務平臺,來協助品保部門做更有效的品質管理。
有了這套訊息服務平臺後,現在,品保人員就能將每一次代工廠商送交的加工零件檢驗完畢後,再將評估報告直接上傳到該平臺上就算完成,而加工廠商得要自行主動來查看內容,加以改善不良的生產項目,品保人員不再以電話來通知檢驗結果,以此來解決品管人員不足的問題。
而為了確保廠商能確實查閱報告內容,這個訊息平臺上還會有設定閱覽期限,廠商得要在一定期間內讀取,不然就再也接收不到,而品保部門每季也會定期公布各類別供應商加工品質的最新排名,促使他們更加重視產品加工的品質。
而在導入這套供應商訊息服務平臺後,孫水文表示,至今,委外加工品質發生的不良件數已明顯較過去改善許多。
自行開發圖面版次管理系統,將圖檔統一集中控管
除了協助品保部門建立聯絡代工廠商的統一溝通平臺外,零件設計圖的版次管理則又是和大工業另一個IT與生產流程結合的例子。
孫水文表示,由於和大一向是以產品代工為主,所以零件設計的CAD圖檔,通常得先由代工產品的客戶這方來提供後,再由生產人員依據這些圖面來自行製造零件或再發包給加工廠商生產。
但這些從客戶所提交的設計圖檔,通常會有不一樣的版本,例如有和上一版不同的製程要求等,所以圖面版次的管理就很重要,一旦產線人員拿錯版本給加工廠商時,就可能造成後續一連串的製程有誤。
但是,如果僅靠著現有的ERP系統目前還是無法做到圖片版次和版次之間的有效管理,而非得要另外想辦法才行。
所以,孫水文後來也自行開發了一套圖文管理系統,可以將客戶提交給和大工業各版本的零件設計圖檔統一集中管理,以避免委外加工廠商不小心拿到錯誤的版本。
另外從距今3~4年前開始,全球掀起了新一批換車潮而帶動汽車市場景氣回溫,甚至近年來,更多的是來自新興電動車市場的需求提高。
而為了要打造出能因應全球爆量訂單大量快速生產的實力,和大工業近年來也開始改變舊有的生產思維,轉而採用更有效率的生產作法,甚至是打造新一代自動化生產工廠,這些都在在加深了和大工業IT與生產製造更密切的整合。
而在新自動化工廠今年下半年上線營運後,接下來,孫水文也計畫將運用IT來持續協助改善每一個生產製造的環節,當然也將採用大數據分析技術,透過分析大量機臺數據資料,來提高工廠自動化的產能。
面對新科技,不盲目推崇而是有需求在評估導入
不過即便有越來越多的新科技都開始在生產製造獲得不錯的發揮,例如、物聯網、大數據等。但孫水文至始至終還是堅信,面對大量新穎科技的出現,對於傳統製造業來說,還是得等到有需求,經過全盤評估效益後,才決定要不要導入,而不是一味的盲目跟風。
而這樣的態度也反應在他這幾年所作出導入伺服器虛擬化技術的決定。即使目前和大營運總部機房內所採用的伺服器數量,連10臺都還不到,並只用在幾個主要應用上,例如ERP、郵件和網站等應用,但孫水文還是認為導入虛擬化技術有其必要。
因為他說,在數量少的伺服器上採用虛擬化,雖然對於減少機房成本的效益並不高,但是透過單機式虛擬化的方式,反而做到了更快速的備份與備援,這是比起減少機房成本所帶來還要更大的實質效益。
所以,再全盤評估分析後,孫水文才決定導入。而目前和大工業已經部份有改用微軟Hyper-V虛擬環境,來執行應用的系統,包括有郵件伺服器、網頁伺服器、防毒軟體設備和資產管理系統等。
CIO小檔案
孫水文 和大工業資訊課襄理
● 學歷:朝陽科技大學資管系學士
● 經歷:1999年進入和大工業後,至今已累積17年的IT資歷,一路從IT基層人員做起,歷經了組長、課長等多項職務,去年更升任了襄理一職,不只要負責公司IT維護,現在更要率領IT團隊,肩起打造新一代自動化工廠IT的重責大任
公司檔案
和大工業
● 地址:臺中市大雅區科雅路12號
● 網址:www.hota.com.tw
● 成立時間:1966年
● 主要業務:汽、機車齒輪、變速箱及傳動零件
● 員工數:約800人
● 創辦人:曾福助
● 董事長:沈國榮
● 年營收:約52億元(2015年)
資訊部門檔案
● 資訊部門主管職稱:資訊課襄理
● 資訊部門主管姓名:孫水文
● 資訊部門人數:7人
● 資訊部門分工:硬體設備維護、軟體開發
● IT預算:約300萬~500萬元
IT部門大事紀:
● 2002年:導入微軟AD網域服務
● 2004年:改用微軟Exchange郵件伺服器
● 2007年:導入QAD ERP系統
● 2012年:建立供應商訊息服務平臺、推出資產管理系統、導入微軟Analyzer商業分析系統
● 2015年:新自動化廠房導入MES生產製造管理系統
● 2016年:更新ERP系統至新版本、嘉義大埔美新廠工業4.0建置
熱門新聞
2025-02-05
2025-01-31
2025-01-30
2025-02-03
2025-02-05
2025-02-03
2025-02-05